Certificates
- EN 9100:2018 and DIN EN ISO 9001:2018
- EASA Teil 145, Reference No. DE.145.0253
- EASA Teil 21 / G, Reference No. DE.21G.0048
- Qualified manufacturer in accordance with DIN 2303 Q2,Q4
Procurement
Tanks
MT Aerospace’s Spacecraft Tank Centre runs a dedicated design and manufacturing facility for satellite propulsion tanks (chemical- & electric propulsion) at its site in Augsburg, Germany. The product portfolio includes:
Monopropellant propulsion tanks (positive expulsion device – PED) with an EPDM diaphragm (silica-free), hydrazine as the catalyst and nitrogen or helium as the pressurant. Diaphragm tanks prevent propellant from sloshing to a great extent and are capable of orienting the propellant even at high disturbance torques and accelerations. MT Aerospace boasts in-house design & manufacturing capabilities for these tanks.
Bipropellant propulsion tanks (surface tension tanks) fuelled with monomethylhydrazine (MMH) and its oxidizer nitrogen tetroxide (NTO). In order to avoid stress corrosion defects in titanium propellant tanks, 1 or 3% of nitrogen oxide (NO) per weight by volume is added to the oxidizer NTO. This mixture is called MON1 or MON3 (MON = mixed oxides of nitrogen) depending on the percentage of NO used. As MT Aerospace does not have the design authority for the propellant management device (PMD), PMD tanks are being manufactured “build-to-print” for all major satellite primes.
Electric propulsion tanks (EP) and high-pressure vessels (HPVs). Electric propulsion tanks are mainly designed and built for xenon applications and HPVs for helium or nitrogen usage. Full design authority lies with MT Aerospace.
For all tanks, MT Aerospace strives to pursue family concepts of the tanks in order to satisfy customer requirements. Furthermore, MT Aerospace manufactures all tanks on site in Augsburg, controlling the entire supply chain such as liner welding, carbon fibre overwrapping with its own filament winding machines (COPV) and tank testing equipment. With its own R&D budget, MT Aerospace develops the next generation of tanks further in areas such as demisable tanks and green propellant applications.
Under a current ESA project called “ViDA” – Verification of Diaphragm Analysis”, a sloshing simulation model for diaphragm tanks has been developed, enabling MT Aerospace to analyse sloshing behaviour for predefined load cases and validate by experiment via mock-up testing.
Diaphragm Tanks
PMD Tanks
High Pressure Vessels (HPV)
High Pressure Vessels (HPV) Helium, Nitrogen & Xenon
High Pressure Vessels (HPV) for Electric Propulsion (EP) / Xenon Tank Assembly (XTA)
ATV Program (Restart Activities Required)
Tanks in Space
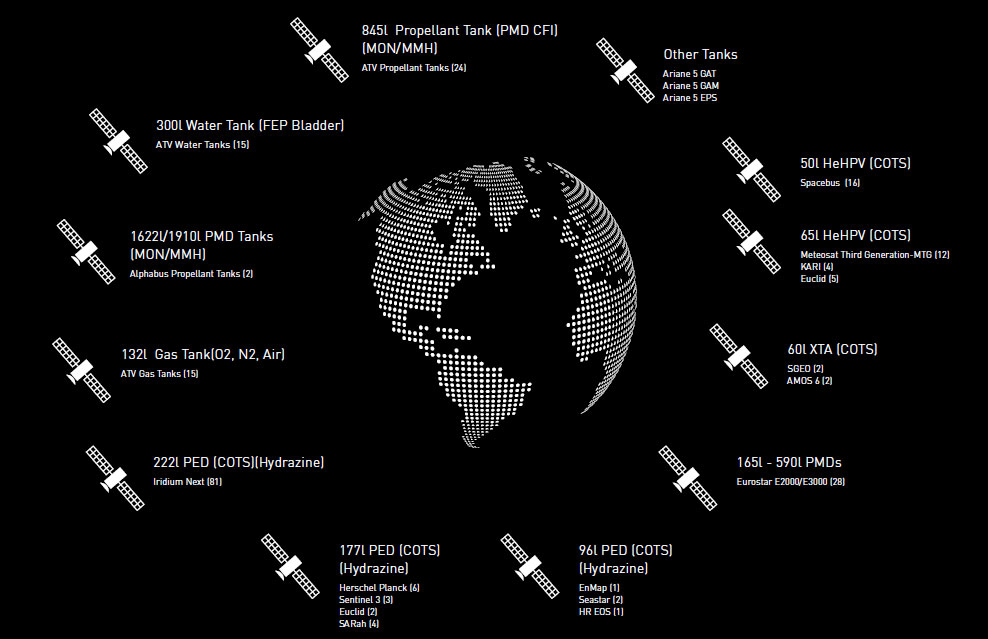